The core of an aircraft engine usually includes hot parts, which are subjected to high temperatures and heavy loads and are easily damaged. Therefore, defect detection needs to be carried out regularly. However, due to the harsh working conditions of these hot components, most detection methods are difficult to achieve. Aircraft engine endoscopes have become an effective means to detect the internal condition of the engine. Visual inspection is an early and widely used detection method in the field of non-destructive testing of aircraft engines. The process of using an aircraft engine endoscope to detect the engine is often called a detection hole in the industry, and the endoscope used is also called a detection hole instrument. As early as 2006, the Chinese civil aviation administration attached great importance to the formulation of relevant testing standards, and in 2009 officially issued the industry standard MH/T3019-2009 “Visual Inspection of Non-destructive Testing of Civil Aircraft”, which included hole inspectors in the scope of qualification certification. It can be seen that the importance of boresight in aviation safety non-destructive testing. The engine endoscope has three obvious advantages: 1. It can detect the internal condition of the engine. We usually find the condition of the outer surface of the equipment easily, but the internal condition cannot be found by the naked eye. Once the machine fails, it is difficult to locate, so how to detect the internal condition is a difficult problem. The engine endoscope has a natural advantage in this regard. In aircraft engine inspection, you can clearly see the cracks, notches, pits, cracks, burns, blade tip edges, blockages and other defects inside the engine. 2. The test results are intuitive. The aircraft engine endoscope reflects the internal condition of the equipment by taking pictures and recording videos. It has the advantages of being real, intuitive and real-time, which is unmatched by other detection methods. For example, ultrasonic testing can determine whether internal corrosion occurs by measuring the wall thickness of the pipe, which is related to many factors such as the coupling state of the ultrasonic probe and temperature changes. Moreover, using wall thickness data to indirectly reflect the corrosion condition often requires a large amount of online data to make a judgment, which is difficult to achieve real-time and intuitive. 3. There are a variety of products. After a long period of continuous development, the technology of this product has become more and more mature, and there are more and more types. No matter what kind of inspection site, there are corresponding endoscope equipment to match. The industrial application of engine endoscopes in aircraft engine maintenance has become more and more mature. Many newly produced engines will reserve endoscope inspection holes, such as holes near the ignition nozzle. You only need to insert the endoscope probe from these holes to the appropriate position to observe the internal situation of the engine. The whole process is real-time detection and intuitive.
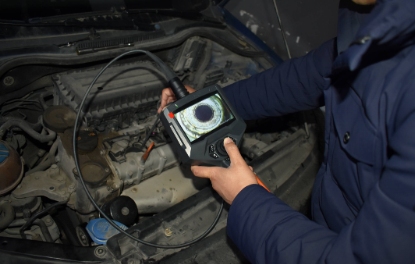